Rose's Roller
(To others who read this, it was originally written for a
friend, and she is
addressed in the text. I've included it for any who find an
interest).
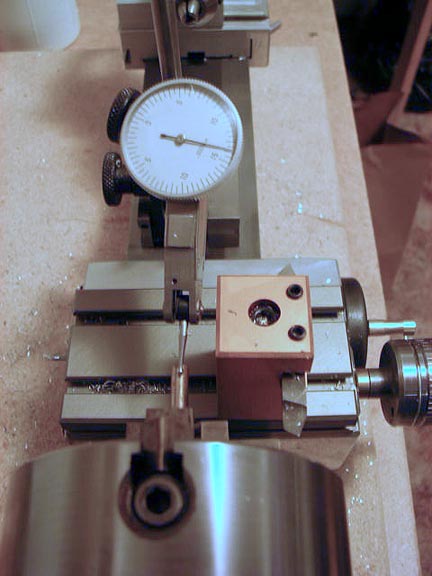
The first thing I did, Rose, was put a piece of stock in the chuck
and rotate it round and round, adjusting the jaws of the chuck
while watching the indicator dial. When it ran true, I was ready
to start.
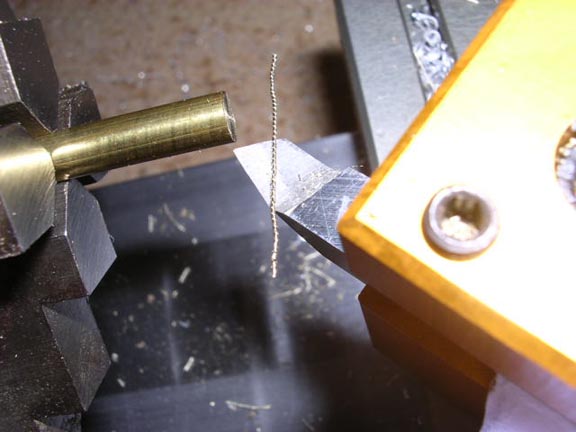
Then mount a cutter in the tool post and face off the end of the work
piece so
it's square with the rest of the lathe.
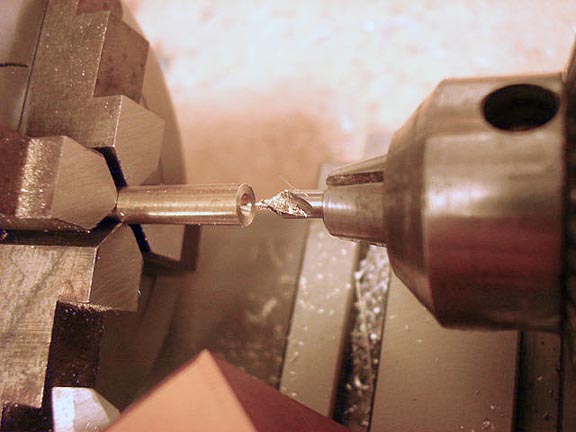
With the end faced off, a small bit called a center drill can put a
hole right in the
center of the end of the work piece. The center drill cuts a
tapered hole that
matches the taper on the dead center on the end (the tailstock) of the
lathe.
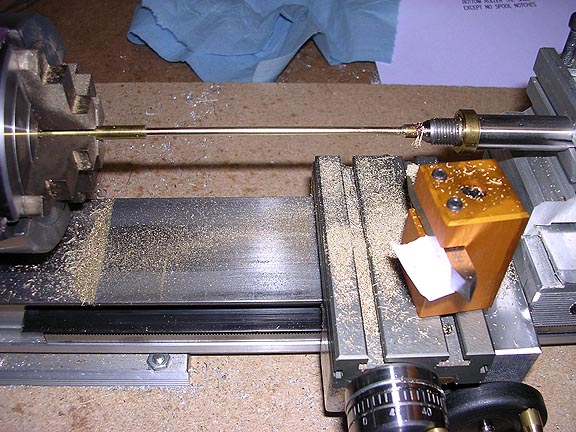
The dead center is the part on the right that is holding the end of the
work piece.
It has a small point at the end that fits into the hole just drilled by
the center drill in the previous pic.
It has to be used for pieces that are long to keep them from wobbling
all over the
place. Without the dead center in the end of the shaft, the work
would climb up
over the top of the cutting bit.
In this shot I've taken a number of passes from right to left, reducing
the diameter of the
work piece to get it down to the size needed. Soon I'll buy, or
maybe make, a follow
rest that will support the long piece as the carriage travels while
making a cut. As it
is, only very light cuts can be made, or the rod will bend away from
the cutter. It will even
then, and if this piece has to be perfectly true from end to end, it
couldn't be done with-
out a follow rest.
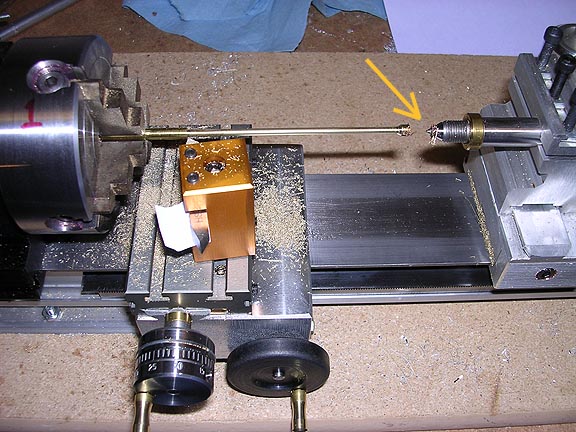
Now I want to cut off the piece that will be used to make the
roller. The dead center
on the right has been backed out of the hole in the end of the
shaft. If it is left in
the hole while the piece is being cut off, there will be bad
consequences. The dead
center is pushing toward the lathe chuck to hold things in
place. Cutting it off with the
dead center in place will cause the cutter to bind and rip the piece
out of the lathe, flinging
it across the room, or into your tender body. I've seen pieces of
metal come flying out of
a lathe because of a mistake like this. Once one went right
through a sheet rock wall.
(That was on a much larger lathe, but still...)
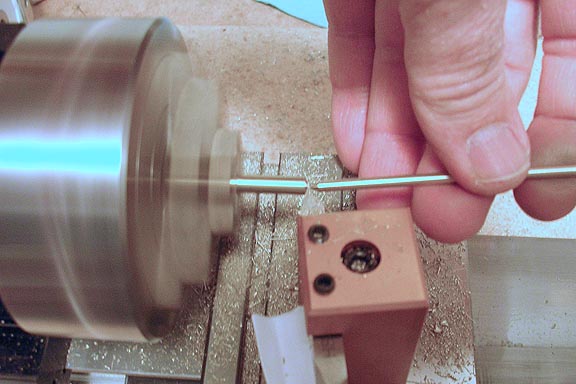
Since this is a small (and smooth) piece, I just hold it with my
fingers as I run the cutting
tool into the work piece stub near the spinning chuck. It just
slices it right off and lies down
into my hand. For a big piece, on a big lathe, you would
use rollers under the work piece
as you cut it off. This is actually called "parting off", and
normally you would use a parting
tool, which looks like a thick knife blade. It is driven into the
spinning work piece, and it
peels off a ribbon of hot metal as it cuts towards the center of the
rotating piece.
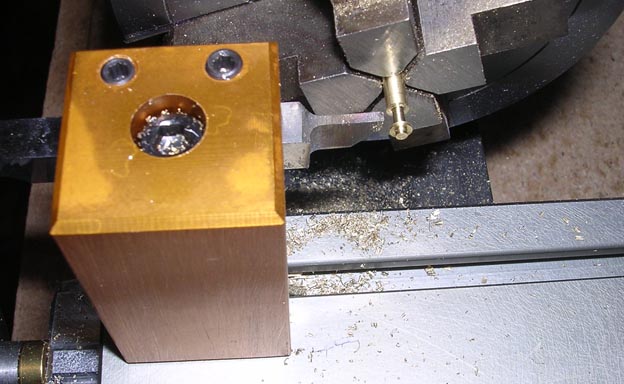
Once the piece is the right length, machining operations near the end
of the piece can be turned
without using the dead center, because it is close enough to the chuck
that it is fully supported
by the chuck jaws. The tool I'm using here is actually a parting
off tool that I mentioned in the
paragraph above. This is a small lathe, so the tool
is sized for it. Just happens to fit the
job at hand.
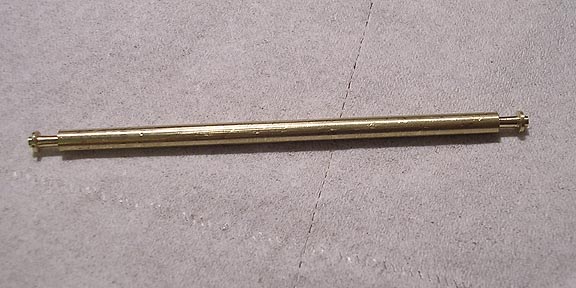
This is what I came up with. I've ordered some parts
that will give me a readout
of the cut length in thousandths of an inch, but it's not here
yet. The Taig doesn't
have any kind of read out for the carriage travel. This part was
actually .004" short.
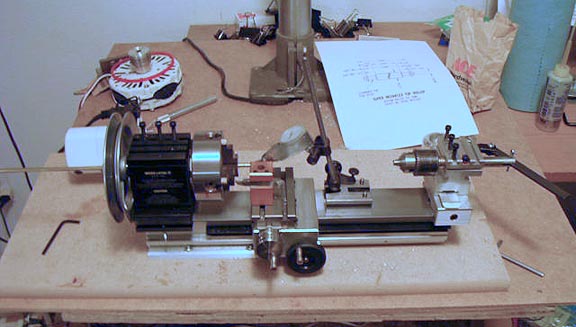
Here's a shot of the complete lathe. Made in America. Very
basic, the way I
bought it, but as I make tooling for it, it will be able to do all the
normal lathe functions.
I just used a sewing machine motor to power it for now. A bigger
motor is in it's future.
This one does fine for soft stuff like brass and aluminum, but won't
sustain a cut in steel
for long, without bogging down.
So,
I got a Taig..
The start of my little machining section.
deansphotographica.com
deanw@bmi.net
May 2007