A Miniature Lathe Chuck
Part 2
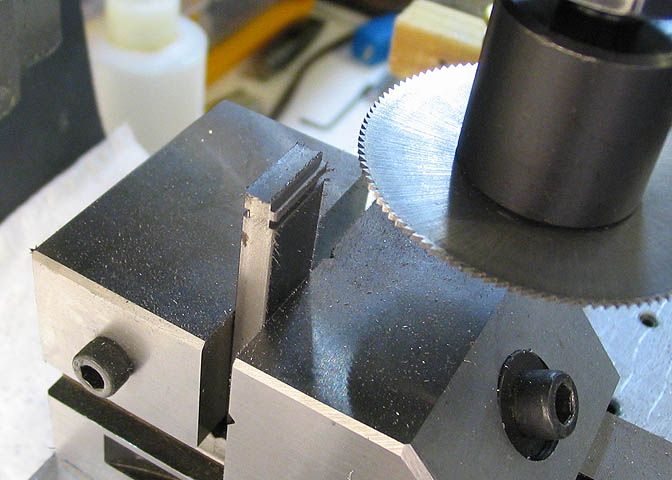
For the chuck jaws I'll use cold
rolled steel. The dimensions on
this kind of steel are generally held
close enough
from the foundry that it can be used as
it comes. In other words, if you
buy 3/16" thick metal it will really be
3/16", or .188" thick, so if you want it
to fit nicely into a slot of that same
size, it will be a nice fit. On
the
other hand, hot rolled steel is often
off the nominal size by .010-.015" and
often has to be brought to size by
milling or some other means.
I started with a piece long enough to
easily hold in the vise, and using a
slitting saw cut in the grooves needed
to match the machining on the chuck
body.

Here's another view of the piece.
The saw does a pretty good job, thought
not quite as nice a finish as an end
mill would make. I used the saw
mainly to save on breakage of miniature
end mills. When they get as small
as
the slots needed for the jaws, they
break pretty easily.
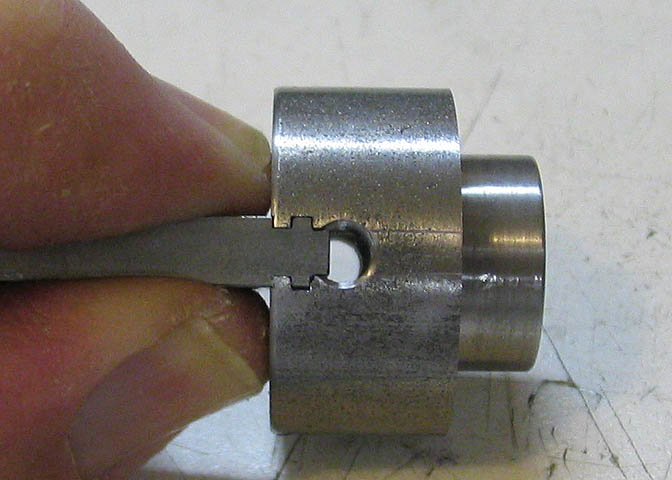
Here's the first try at getting the jaw
piece into the chuck body. I spent
a bit of finish time with a file
getting rid of the burrs left in the jaw
and chuck body that were left from the
machining steps.
This one was just used as a test piece,
to make sure my dimensions were on
before I make a matched
set of four jaws.
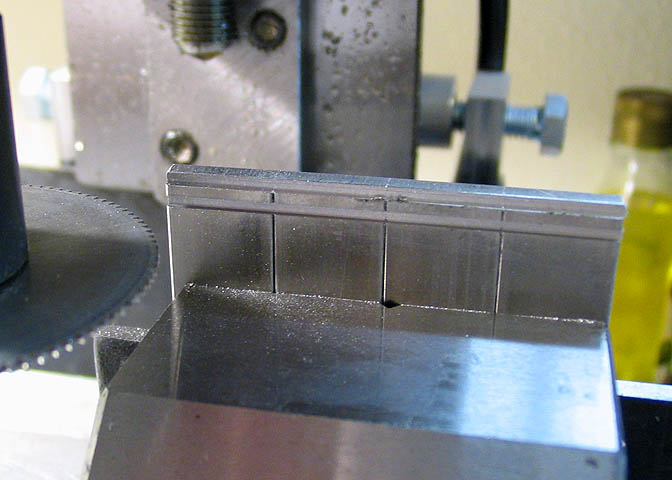
Now
that I know I have the correct
dimensions for the sliding part of the
jaws, I set up four pieces of steel
in the mill vise so I can make them all
exactly alike.
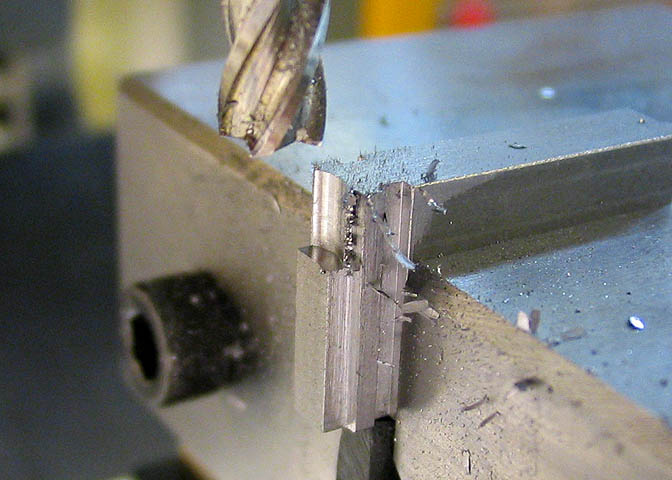
Then each piece is milled for a radius
that will match the jaw screws.
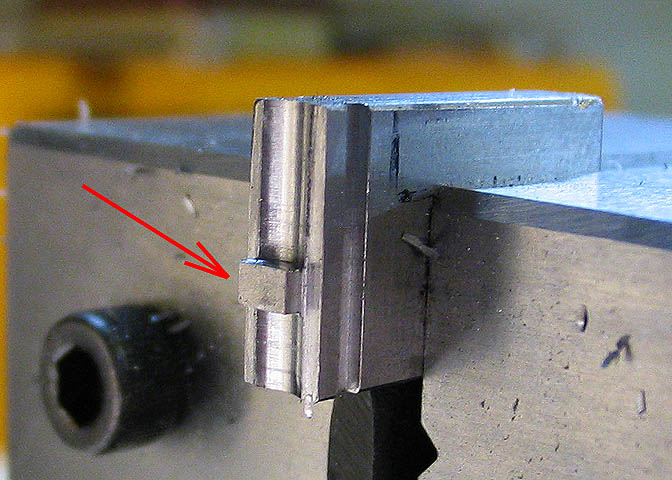
Turn it over and mill the other
side. The block looking piece that
is left will be the drive lug for the
jaw screws.
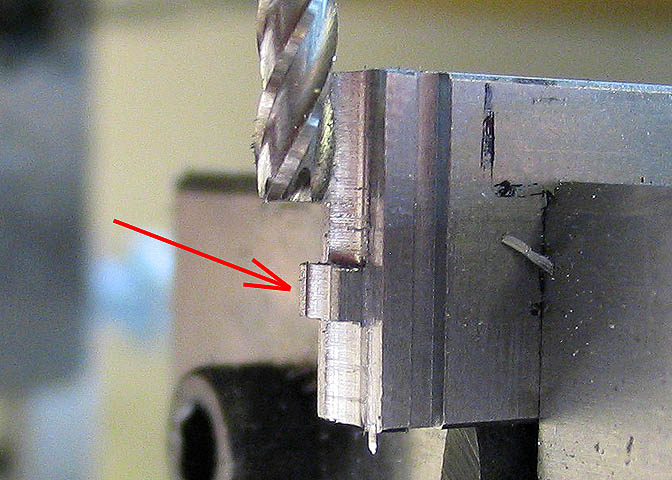
A small radius is milled into that block
that will fit over the driving slot in
the screw.
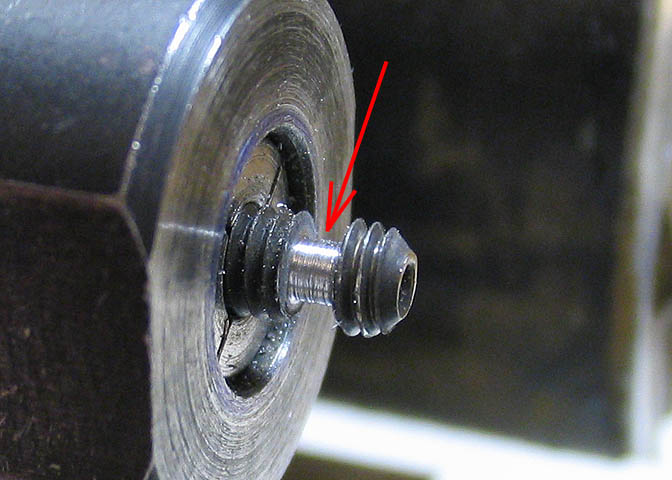
This is the driving slot cut into one of
the jaw screws. I'm using 10-32
hardened set screws for this.
The cutting tool has to be good and
sharp to cut them. On this one, it
wasn't sharp enough, and left
a rough surface inside. Time to
break out the Arkansas stone and try
again.
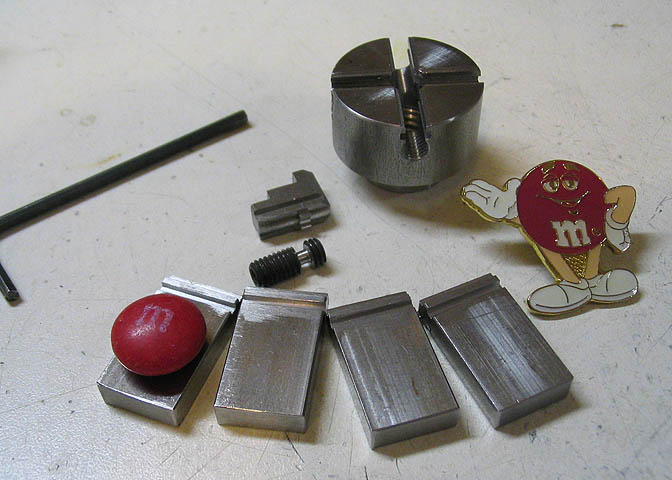
Here, you can see the jaw blanks, along
with the one finished test jaw and drive
screw.
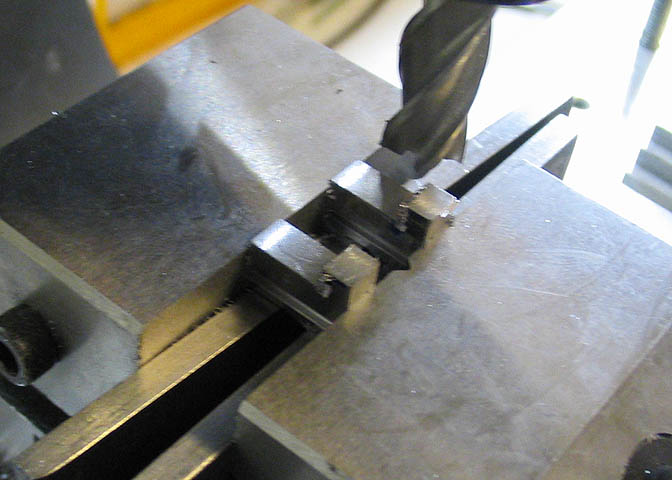
Cutting the steps in the jaws is
easy. Apparently, getting a sharp
picture of it was not... Sorry.
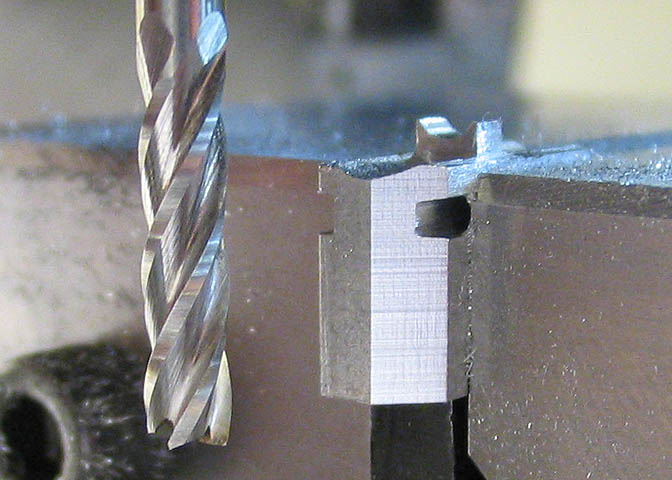
Then the ends of the jaws have to be
beveled, so they come to a point with a
small flat in the middle
of that point. The mill vise was
set to 45 deg, and one side cut using
the X travel on the mill table.
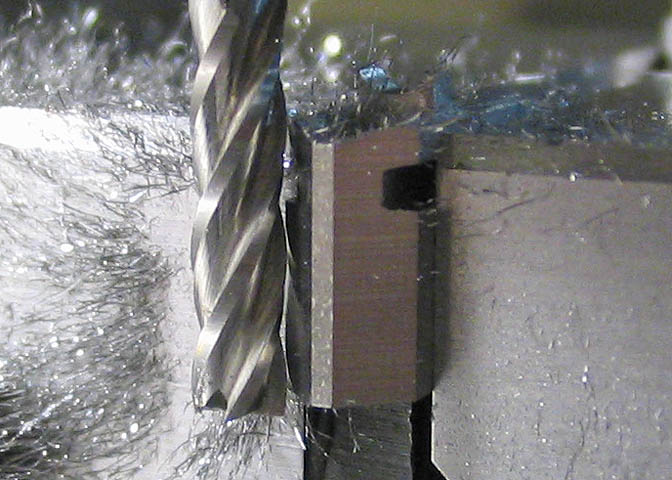
Then the other side is cut using the Y
travel of the mill table. To get
the angles the
same width on each side I counted how
many thousandths in-feed I went on the X
table travel, then
cut the same amount on the Y table
travel. Once I had as much left in
the middle that looked right, I
wrote down the figures, then did the
other three jaws the same way, so they
all look alike.
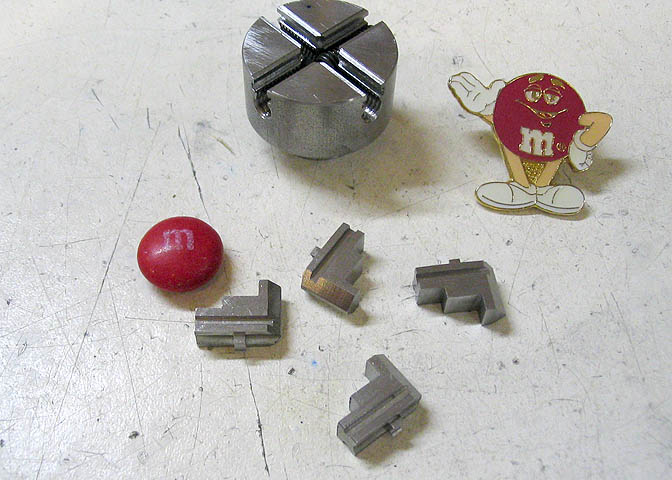
And finally, they are done!
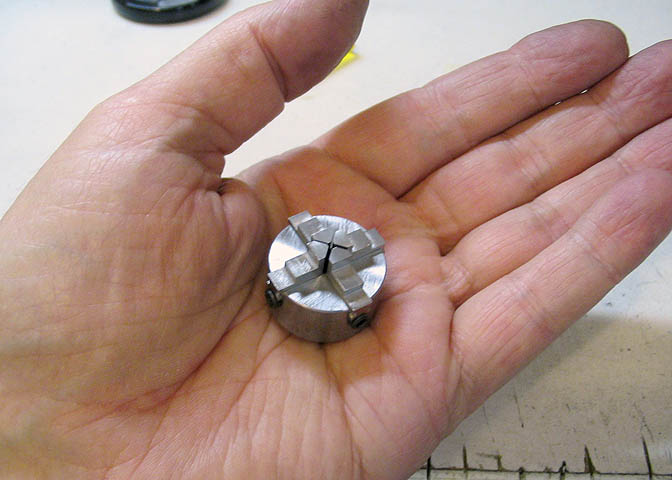
Not bad, I guess. Looks about like
a chuck, to me.
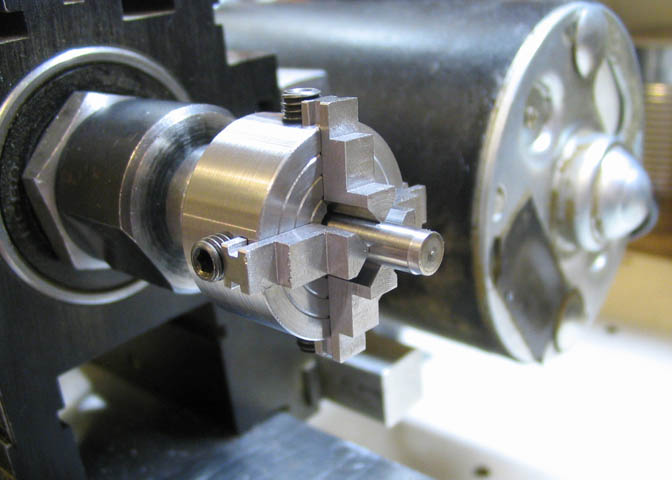
I put Kenneth's new spindle in my small
lathe and screwed on the new chuck to
check it out.
Works just like the big boys.
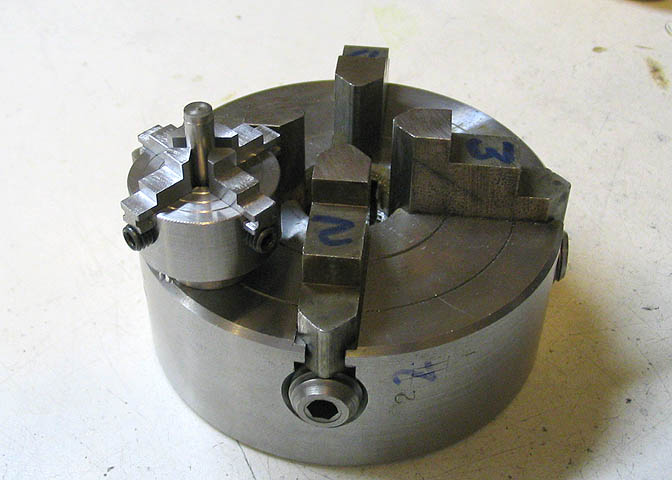
Here it is with the chuck it was modeled
on, the stock Taig four jaw.

With the M&M machinist's scale.
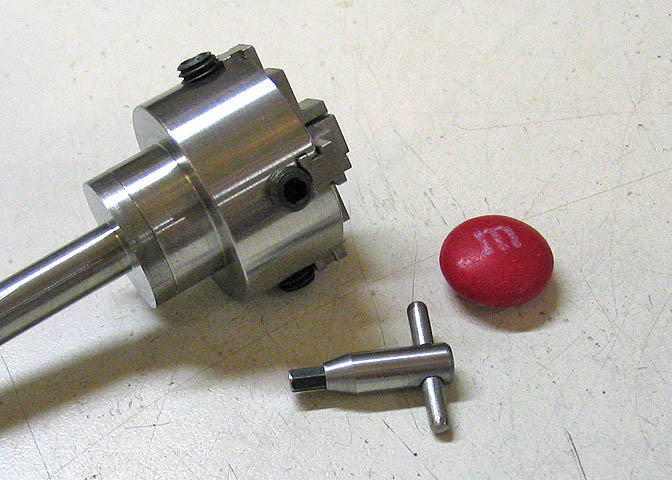
Of course, it has to have a chuck
key. The key was made from drill
rod, and the hex end was cut
from an Allen wrench. Then the
piece of hex is pressed into the key.
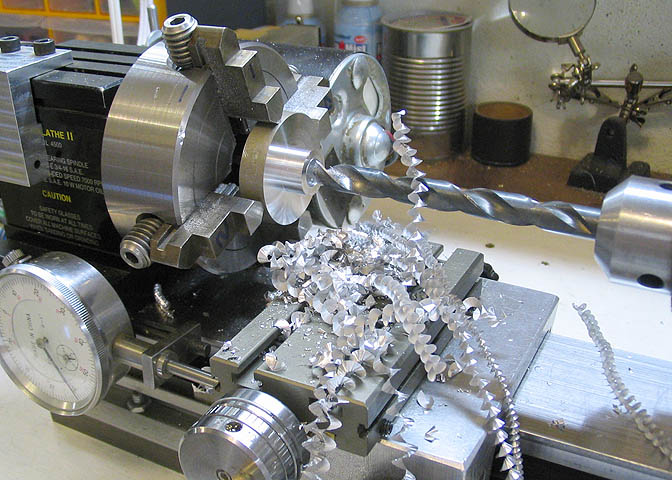
I figured while I was at it, my friend
could also use a miniature face plate
for his model lathe.
This part is made from aluminum.
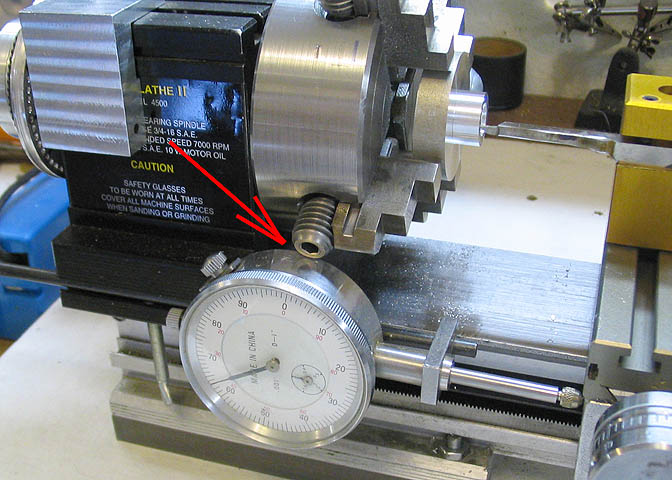
Thought I'd show this while I'm at
it. While I don't find Chinese
made end mills to be very good,
they do make acceptable dial indicators,
which also happen to be very
cheap. Cheap as in, if I
bash it with something like a chuck, I
won't feel as bad as if I did the same
thing to my nice Starrett.
Obviously, this was my own fault!
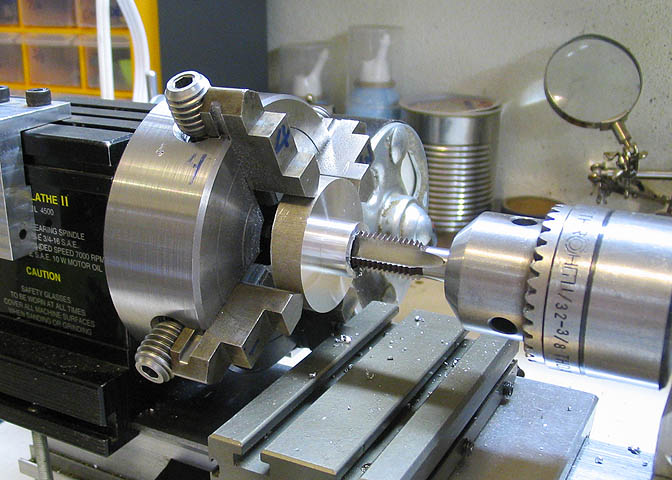
After boring a hole in the face plate,
it's tapped for the same M12 x1.5
threads as was used for the chuck.
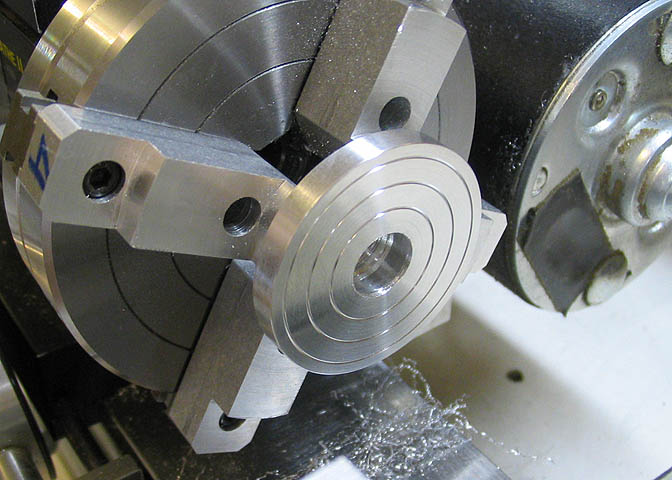
Then it's flipped end for end and the
face and diameter cleaned up, and
centering rings cut in.
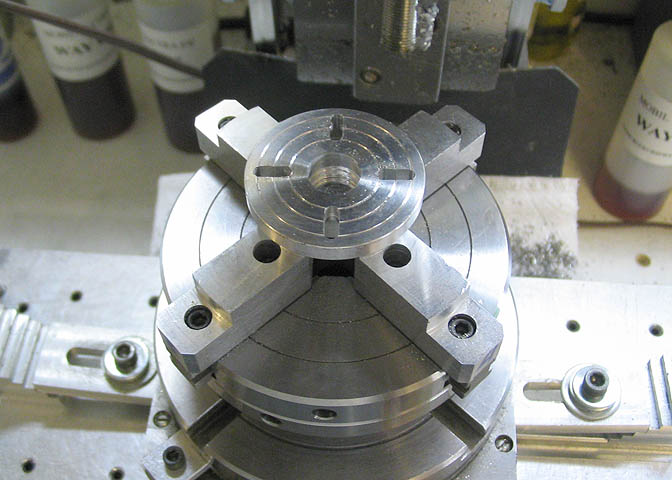
Finally, some slots are milled for
clamping hardware, and this last piece
is done.
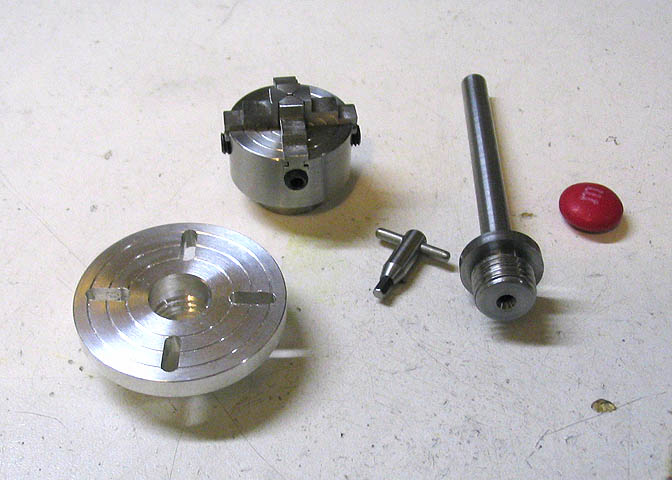
That's it for another project.
These pieces have since been shipped off
to Denmark, and friend Kenneth
now has a little model lathe that is
fully equipped.
Thanks for having a look. Hope you
found something worth reading.
Back
to Part 1
To go back to
the main projects page, click the link below.
More
Taig Lathe & Mill Projects
Copyright 1998-2012 Dean Williams