Compound Slide/Milling Attachment
Using the Taig compound slide
as a milling attachment for the Taig lathe.
The compound slide for the Taig will do a good job as a milling
attachment too. You have to rig up a few
things and make a few parts. It's an enjoyable day of doodling.
(Of course, if you don't want to doodle, you can just buy the factory
Taig milling attachment.)
The first thing you need to do is remove the swivel on the bottom of
the compound. It's easy to get off.
Take a look at it. You'll figure it out.
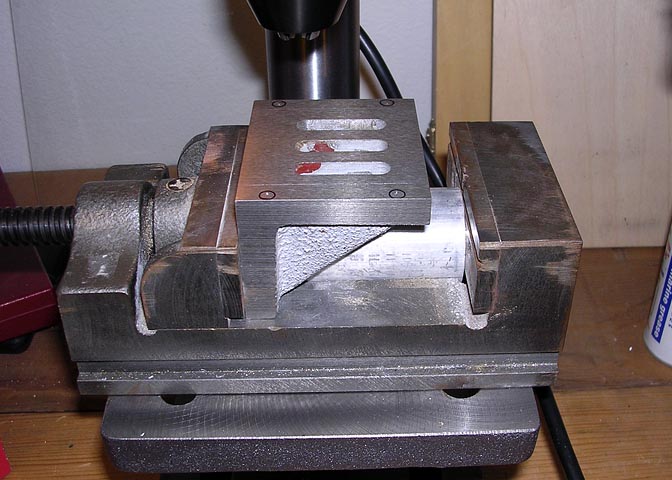
You'll need something to hold the compound in the vertical position to
use it as a milling attachment.
I had this angle plate that I got from Enco a few years ago.
They're only about $7, and ground at a 90 on
the finished surfaces. Here I have four holes laid out on the
long leg of the angle plate. I'll drill them to
take 10-32 machine screw threads.
To be truthful, I have the angle plate in the vice the wrong way 'round
in this shot. The flat leg of the angle
should be against the fixed jaw of the drill vise. That will keep
everything square(er).
Lay your compound slide on the long leg of the angle to lay out the
holes. The size plate I used is
2 x 2-1/2 x 3". One leg is 2" long, one 2 1/2", and it's 3" wide.
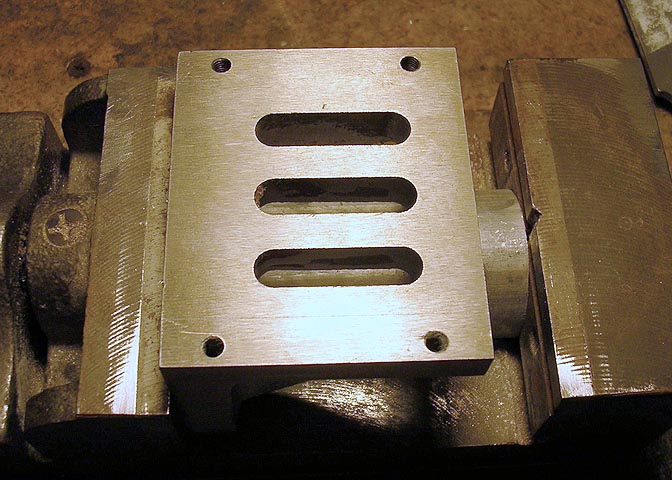
Drilling and tapping is done in this shot. The plate is of cast
iron. Easy to drill, easy to tap.
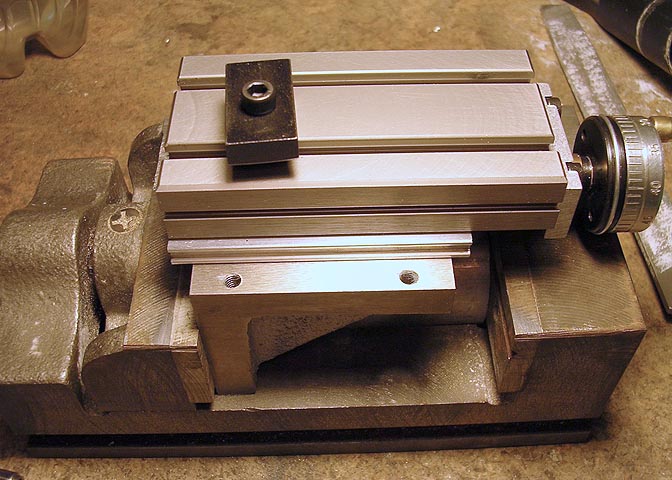
This is how the compound will sit when mounted to the angle
plate. A piece of flat stock will go into the slot
that is milled into the edge of the compound base. A couple of
shim washers under each side of the flat
stock on each side and a 10-32 machine screw in each hole will hold it
just fine.
The small block at the bottom of
the slide is the tool holder that is used when using the compound
for it's original purpose. It comes right off..
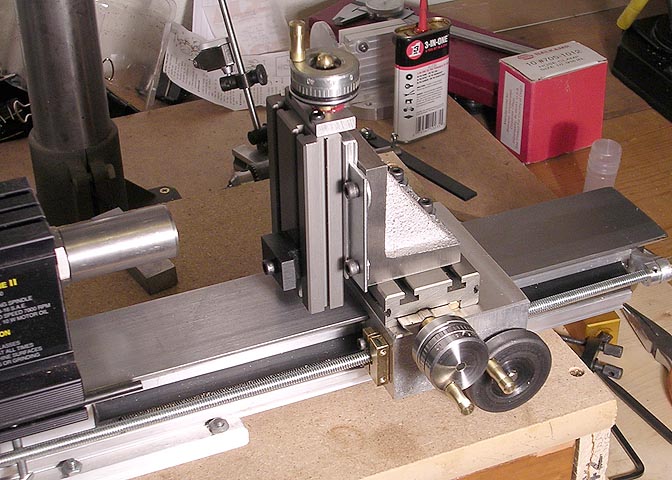
Here's a shot of the compound as milling attachment. But, nothing
to hold the work piece, yet.
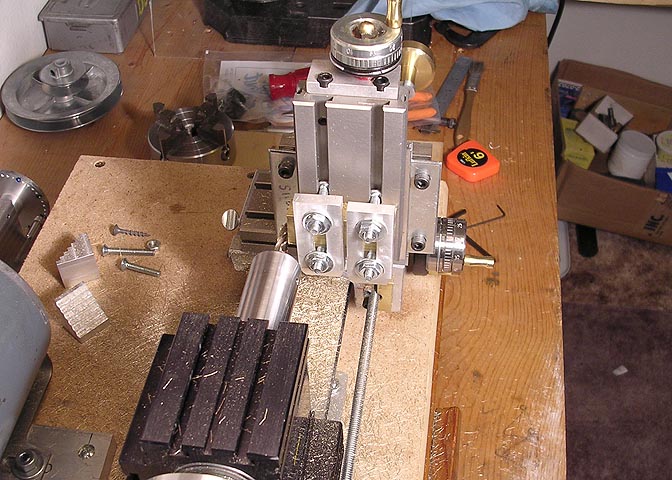
I need to make a couple of jaws or blocks that can be attached to the
slide. I'll make something very similar
to the regular item that Taig furnishes. I made these of 1/2 x
3/4" brass stock, since I had some handy. Unless you're
really going to do some heavy hogging, even aluminum should do
fine. You could use steel too, of course.
Here I've got one of the brass blocks held to the slide with a couple
of finger plates I made a few years ago.
Just milling the ends off square, and to a length of 2".
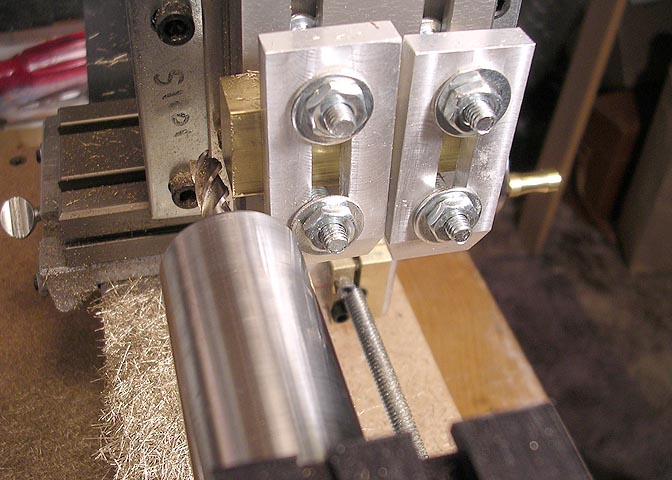
A close up, for detail.
Milling needs to be done so the cutter cuts against the feed. In
other words, this shot was taken after the
cut was made. The mill rotates clockwise in this shot. The
work piece needs to start below the cutter
at the beginning of the cut, and the mill table is cranked upward, so
the cutting edge of the mill is cutting
into the work piece as it
travels. You're asking for trouble if you feed the work piece
into the miller in the same
direction as it is rotating. Think about it. The mill will
want to suck the work piece into it's cutting edges.
That can cause problems, particularly for small machines.
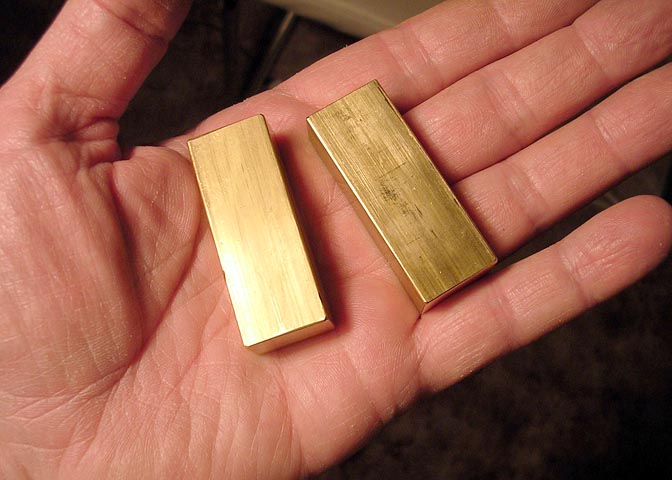
Once I had the ends squared up I gave the edges a little touch up with
a fine cut file.
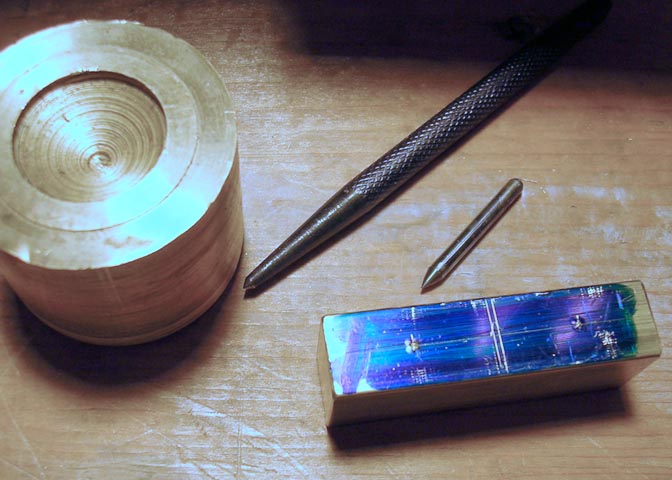
Now mounting holes are laid out. The center of the holes needs to
be in line with the T slots on the slide
so they will mount up. The thing on the left is a whacker.
It's taking the place of the brass headed hammer
that I haven't made yet. Soon...
I drilled out the needed clearance and tap holes, filed things up
smooth and shiny and mounted the
two blocks on the slide.
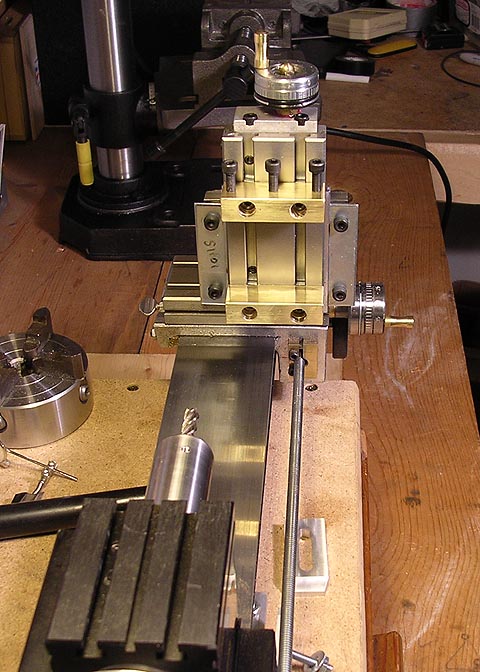
Looks like this now. Very much like the way Taig does it.
(No use re-inventing the wheel!)
More (Taig) lathe projects
deansphotographica.com
(homepage)
copyright Dean Williams
6/07